Mesure de l’ancienne pièce, conception et impression de la nouvelle pièce.
Après avoir pris les mesures de la géométrie de la pièce cassée, la création d’un modèle 3D sous Catia devient facile . Quelques modifications de conception ont toutefois était faites. En effet le procédé de fabrication de la pièce d’origine (injection plastique) imposait des règles de conceptions particulières (épaisseurs constantes de l’ordre du mm, congés, dépouilles ….) qui n’ont pas besoin d’être reproduit sur la nouvelle ! De plus cette nouvelle conception permet d’augmenter les épaisseurs, augmentant ainsi la rigidité.
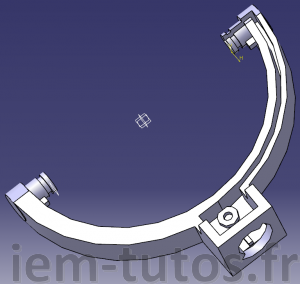
A noter que des passages de câble supplémentaires ont du être réalisé évitant ainsi de dessouder les fils (pas sur la partie reliée au « serre-tête » qui sera assemblé pendant l’impression : cf suite).
Les fichiers sont disponibles sur Thingiverse.com :
http://www.thingiverse.com/thing:606851
Une première impression de la pièce permet de calibrer les dimensions mesurées (obligatoire à cause des incertitudes de mesures et des défauts liés à l’impression).
A noter qu’un passage de fil n’a pas été réalisé sur l’appui carré du bras du casque sous peine de fragiliser la pièce. Il faut dans ce cas, soit dessouder le câble, soit pendant l’impression mettre le câble dans la partie circulaire (ce qui sera fait ici) ! Ce n’est pas simple puisqu’il faut attendre que le bas de la pièce soit imprimé et insérer le fil sans le faire toucher la buse d’impression (sous peine de le faire fondre !). Il ne faut pas interrompre l’impression mais la ralentir. C’est le point critique de la réalisation de la pièce.
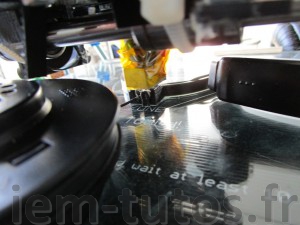
L’impression dure 30min environ et du PLA est utilisé bien qu’il aurait été préféré d’utiliser de l’ABS pour sa résistance mécanique plus grande. Épaisseur des couches en 0.2mm et utilisation des supports en automatique.
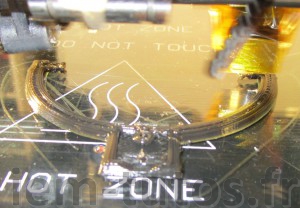
Fin de l’impression :
Il faut un peu épurer la pièce des quelques défauts et des supports en les grattant avec un couteau. Le trou de la vis est trop petit ! La pièce de verrouillage du « serre-tête » sera finalement collée.
Au total la fabrication a nécessité 5 itérations !
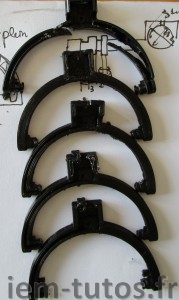
On commence par monter la pièce dans le « serre-tête » du casque avec la pièce en plastique. Cette pièce sera collé ultérieurement.
Puis on clipse l’autre partie dans le haut-parleur :
Ne pas hésiter à roder les liaisons qui sont un peu dures au début. Un dernier test de son pour prouver que celui-ci fonctionne avant de remonter entièrement le casque. C’est repartis pour 4 ans et plus !
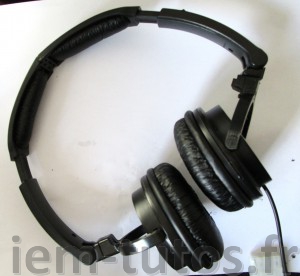
2 réponses sur « Réparation bras plastique d’un casque JVC ha-s360 2/2 »
Merci pour ce fichier
Serais t-il possible d’avoir la version gauche?
Merci
Bonjour,
La partie gauche n’est-elle pas tout simplement le symétrique de la droite ? Auquel cas il suffit juste de faire une transformation miroir dans le slicer !